At Harper Collective, we understand that perfection is not always attainable in manufacturing, but we believe in continuous improvement and innovation to produce better and more sustainable products for our customers.
Our passion for creating functional and beautiful products from "trash" has led us to share our entire sourcing process with others, promoting full transparency in our operations.
Five years ago, we set out to create a luggage line made from sea plastic and post-consumer recycled plastic. Despite making numerous mistakes along the way, we persisted in our pursuit of this dream, designing our cases and logo and beginning the long process of bringing our vision to life.
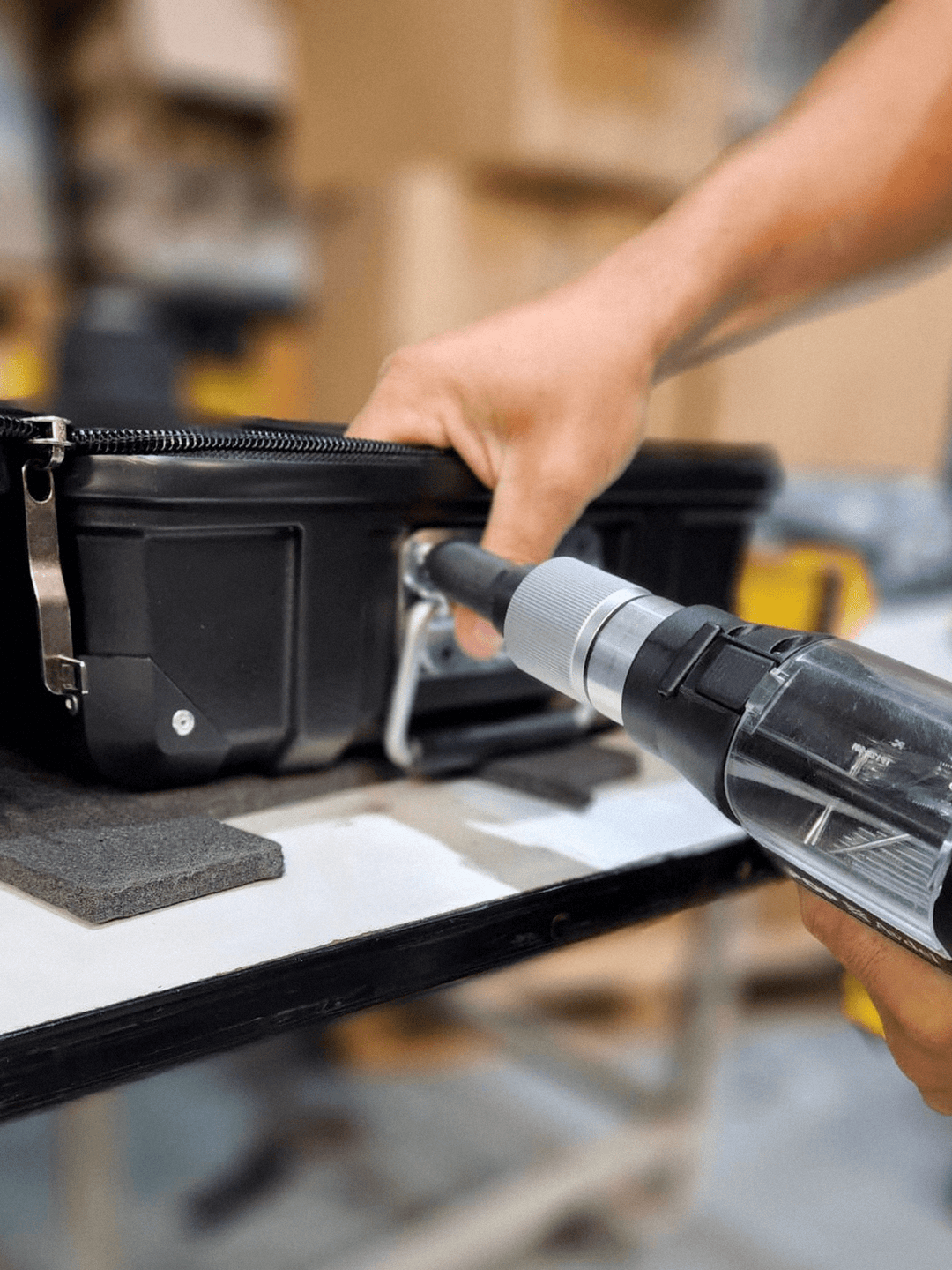

Fortunately, we received incredible support from Phil, our project manager who brought 45 years of experience in luggage manufacturing to our team. His expertise was a game changer for us as we navigated the complexities of the technical category of luggage.
Throughout the years, we developed each part of our product from scratch, learning and growing with each step along the way. Our commitment to sustainability and innovation continues to drive us forward, as we strive to create products that are both functional and environmentally responsible.
At our production company, we have a strong passion for oceans and water. In line with this, we embarked on a mission to study the recycling of fishing nets, a material that often ends up in our seas and contributes to the growing plastic pollution problem. After years of conducting research, trial and error, we made a significant breakthrough.
We partnered with Epsotech, a company based in Germany, to develop a new product using Sea plastic, a revolutionary technology that had never been used before for a luxury product. This new development was a significant milestone in our journey towards sustainability and eco-friendliness. We believe that by adopting such innovative solutions, we can help reduce plastic waste and contribute to creating a healthier planet for future generations.
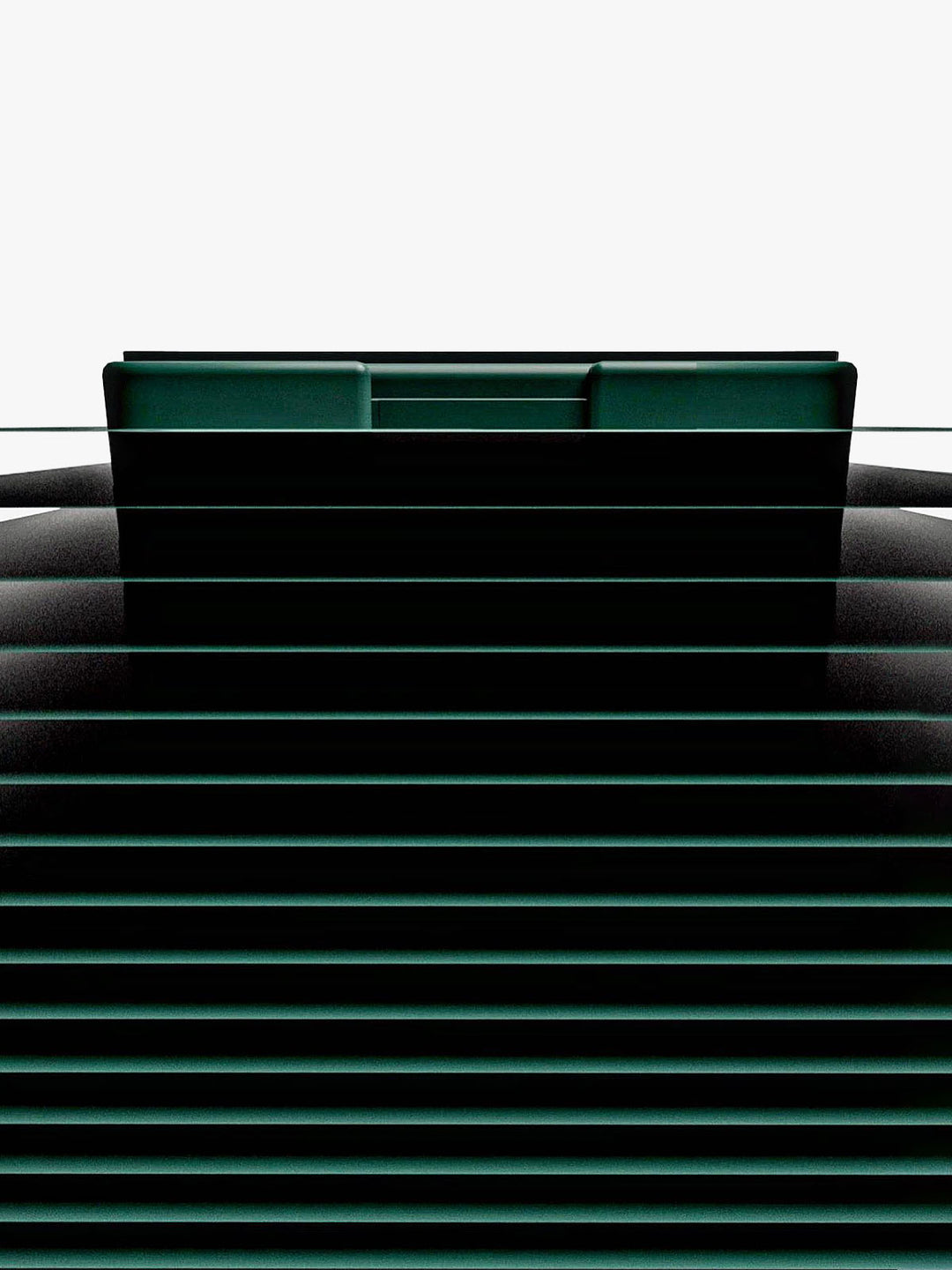
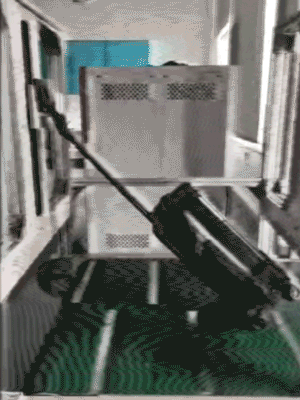
SEA PLASTIC and recycled plastic is hard to form as there is so much different origins and contamination.
We therefore approached the biggest expert in vacuum forming in the England. LineCross in Leicester has been a tremendous partner for our development.
After many years of failure, we cracked it in the autumn 2022, we finally managed to mould our product successfully. But also tested the resistance shock impact and both were successful.
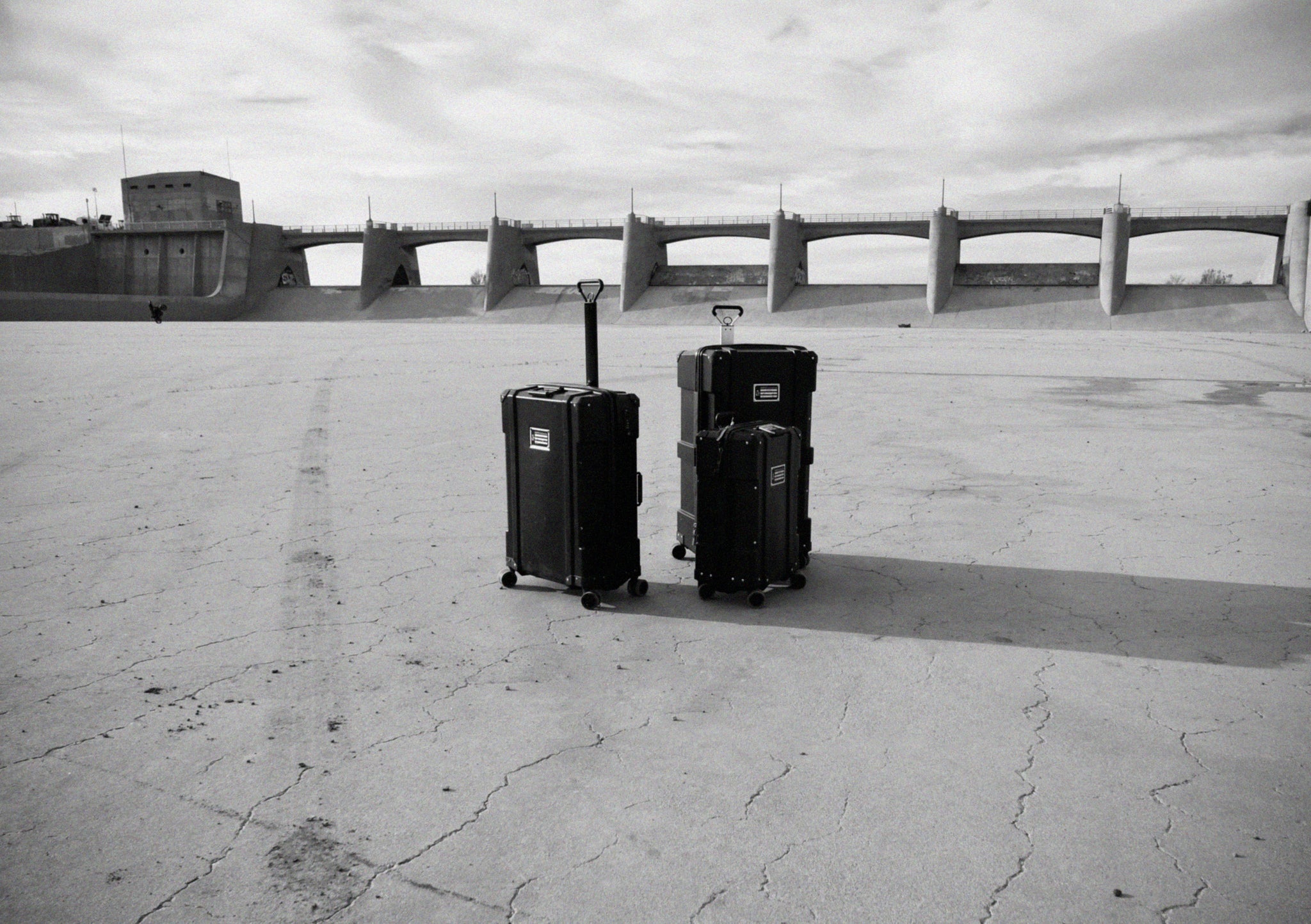
Developing a product from SEA PLASTIC and recycled plastic proved challenging due to various sources and contamination.
To overcome this, we sought out the leading vacuum forming expert in England. Line Cross in Leicester became an invaluable partner in our journey.
Despite years of setbacks, we finally achieved a breakthrough in autumn 2022 when we successfully molded our product. Furthermore, we conducted shock and impact resistance tests, both of which yielded positive results.
At our workshop in Blackburn, UK, we take pride in crafting every case by hand. We're committed to using traditional techniques to ensure the highest quality for our customers.
That's why we've formed a partnership with VGTEC to help us achieve our goal. Together, we're dedicated to creating products that are not only beautiful but also sustainable and environmentally friendly.
One of the ways we achieve this is by avoiding the use of glue or chemicals in our cases. Instead, every component is carefully riveted and stitched by hand to create a durable and long-lasting product.
When you buy one of our handmade cases, you can be confident that you're supporting local craftsmanship and getting a product that's built to last.
Our interior features a special collaboration with the legendary British brand Barbour.
To enhance the look, we have incorporated their signature diamond quilted trim, made from eco-friendly recycled nylon.
We've also added a zipper for convenience, allowing you to easily dry clean your Barbour trim whenever necessary.
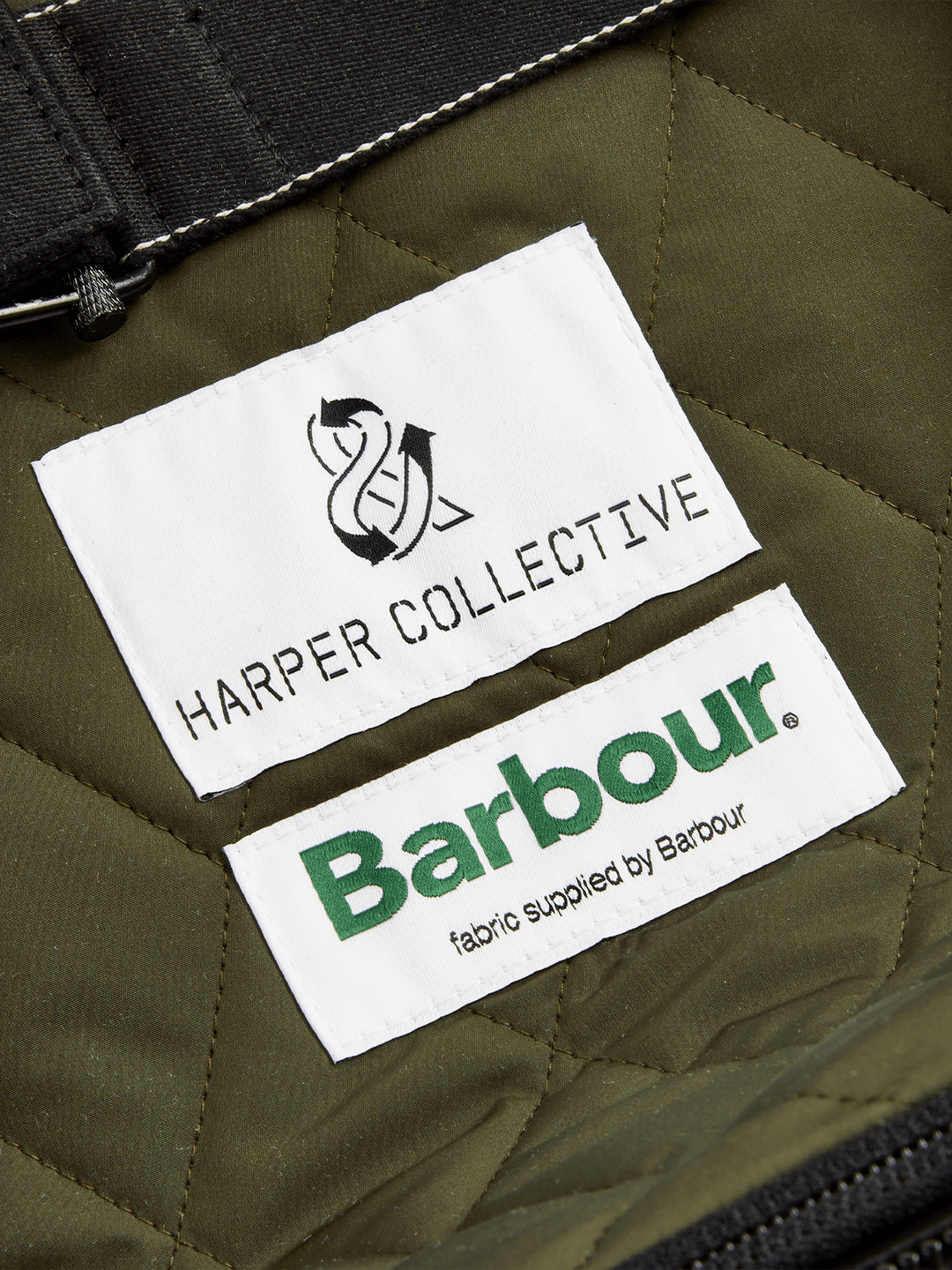
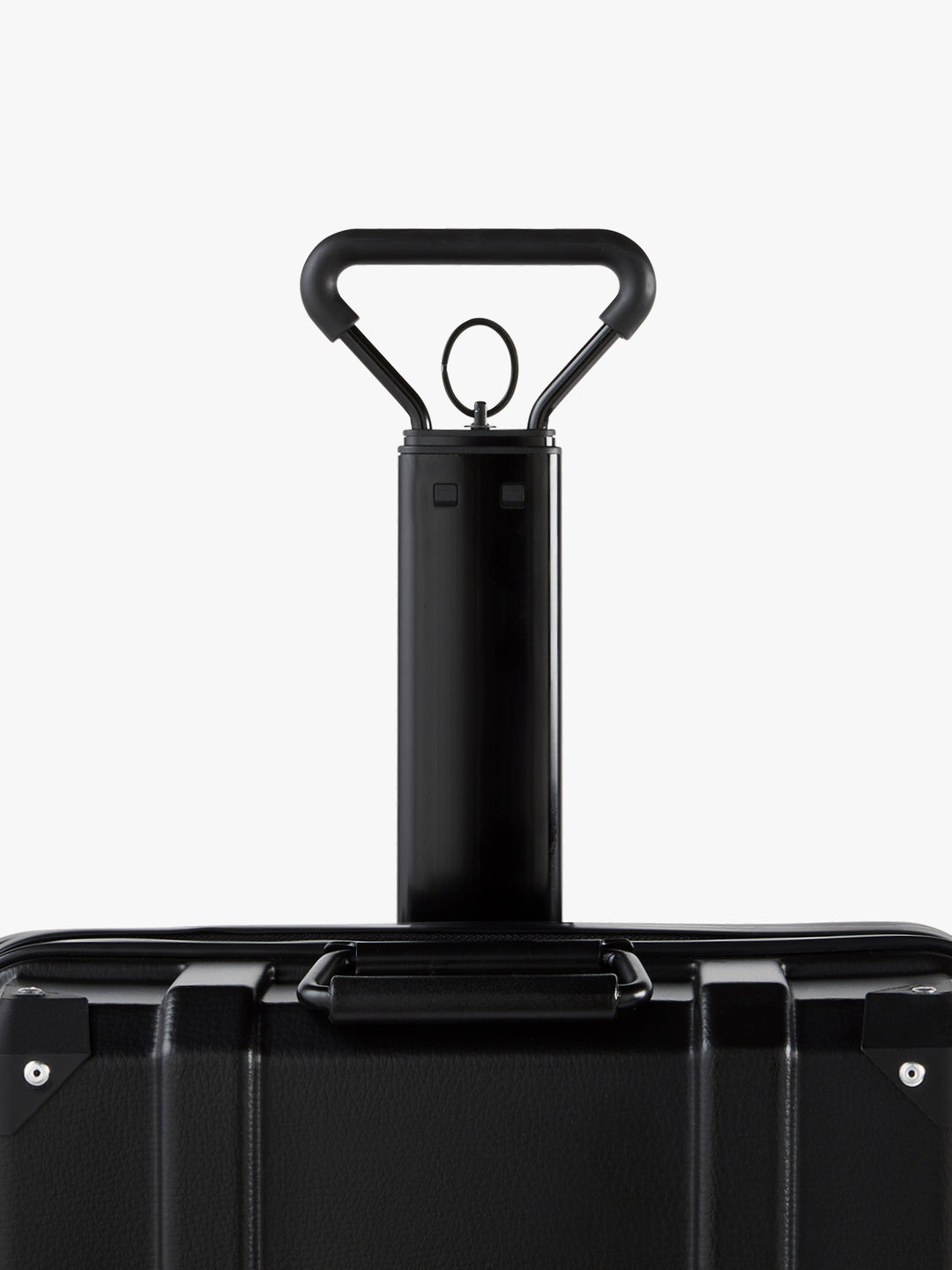
Our distinctive telescopic handle was initially developed in the UK, but production was impossible due to our complex design.
So, we partnered with Jollying in Guangdong China. Same for the wheels which are made from virgin plastic for durability.
Jollying is the perfect partner to deliver the quality required and their expertise and reactivity helped us to deliver our innovative design.